Investigation of fluting on six 1.5 kW induction machines under parasitic and injected bearing currents and improving a LabVIEW program for measuring the bearing currents
Masterarbeit
Background
In inverter-fed electrical machines, parasitic electrical currents may flow through the bearings. This bearing current may damage the bearing surface e.g. fluting. Fluting causes mechanical vibrations in the bearing. Hence, the motor needs to be disassembled to replace the bearing, which is relatively expensive and reduces the reliability of the drive. Therefore, it is of interest to know, which factors influence the fluting.
In typical application, as an example, a rotor connection to the ground via a mechanical load provides a path for the common-mode current of the inverter-fed machine. This type of bearing currents lead to fluting for enough big apparent bearing current densities i.e. Jb.> 1 A/mm².
Tasks
- In this work the effect of bearing current type on the fluting is investigated on six 1.5 kW induction machines at rotational speed n = 1500 /min. For comparison, the assigned bearing current stress for all the cases is the same. The bearing current stress is the integral of the apparent bearing current density over the operating time.
- There is a LabVIEW program written for measuring the parasitic bearing currents. At each measurement, 250 current events are captured based on the set trigger and stored. The program has some shortages. The improved version must able to calculate the bearing stress and to store the trigger and the time distance between the measured signals. A search trigger must be implemented to capture the 250 events within the specified time.
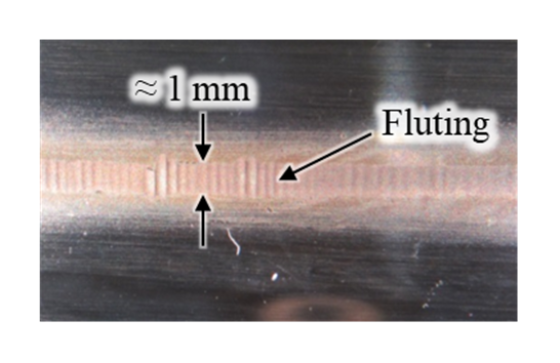
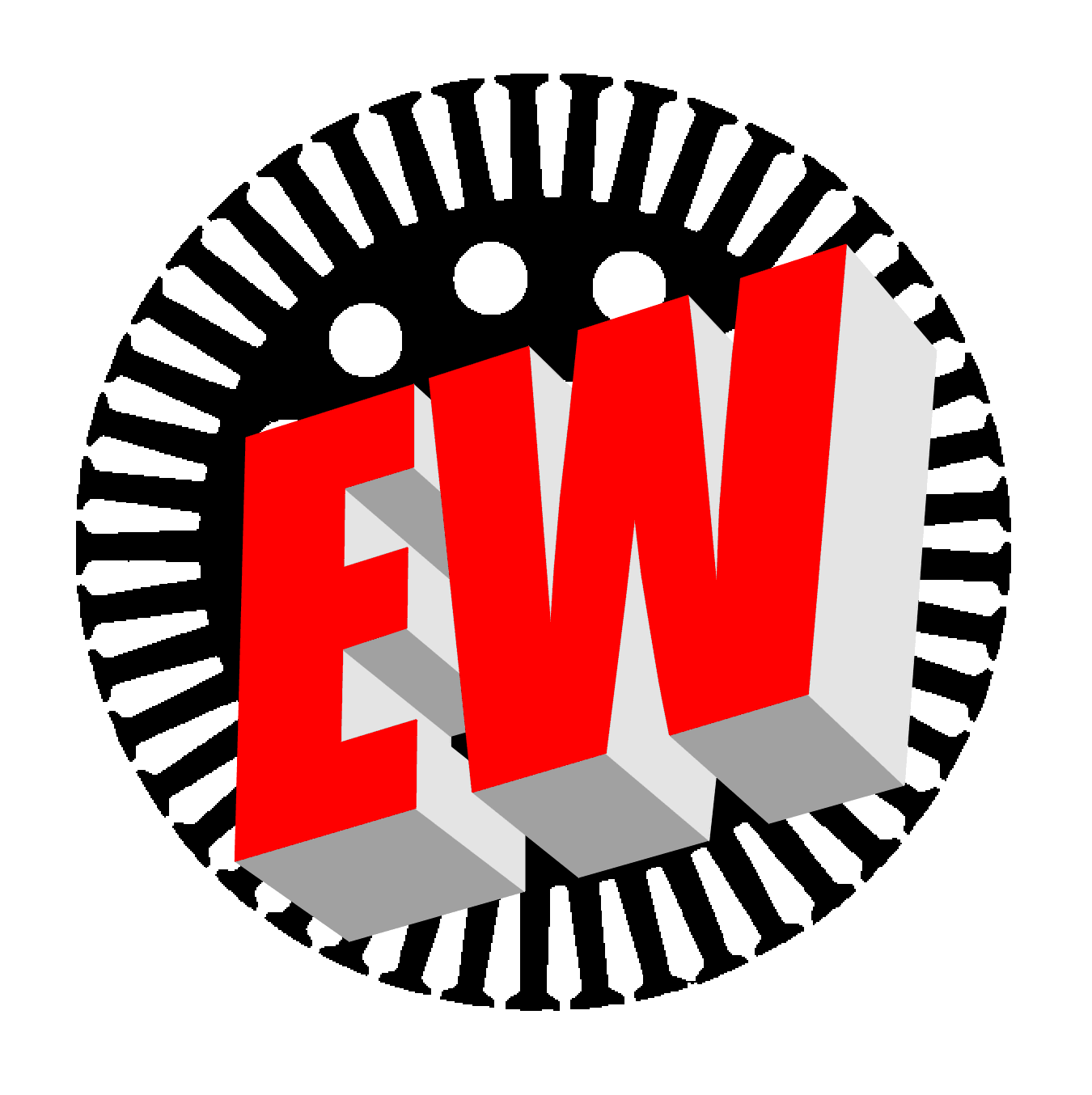